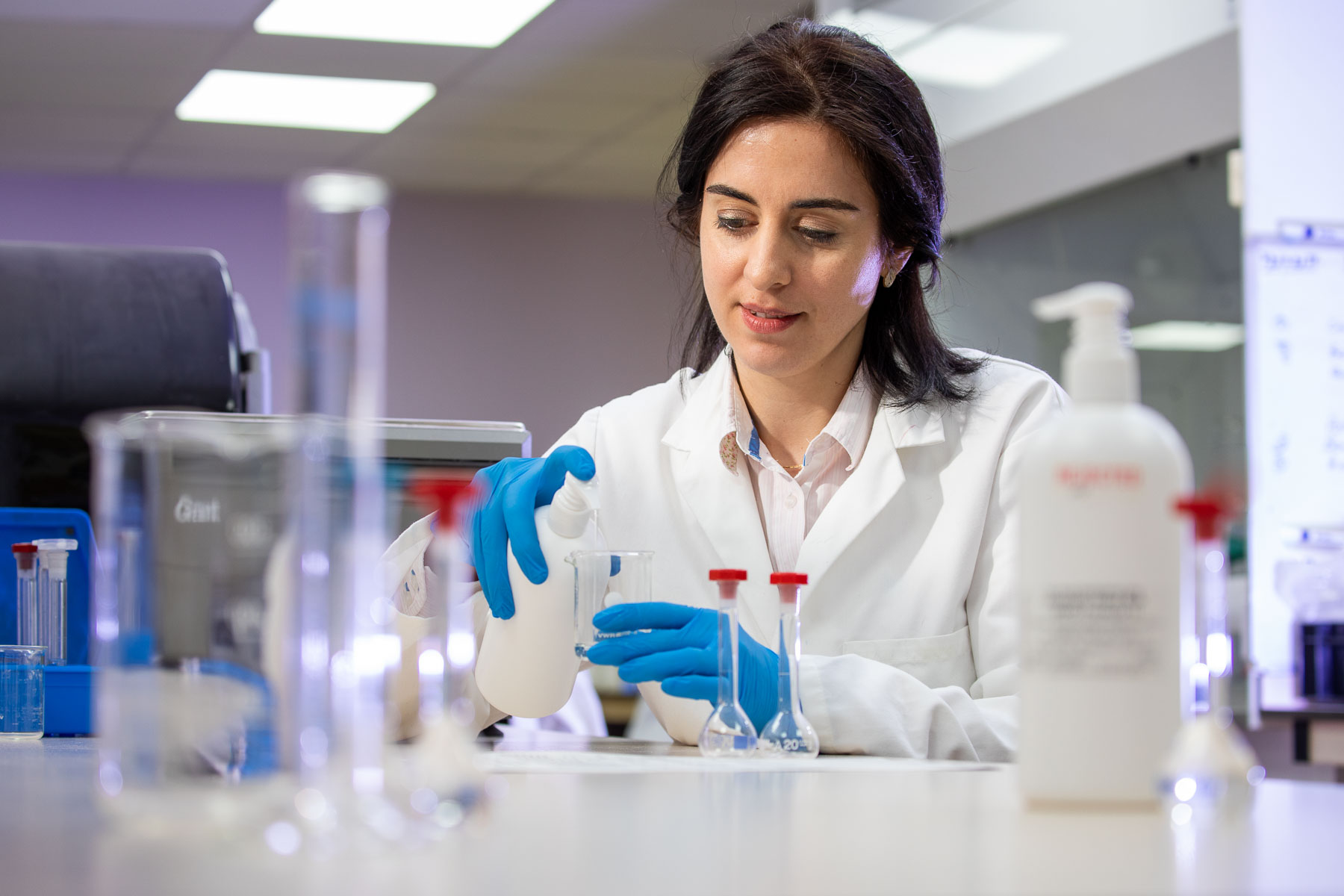
A production line for hand sanitiser was set up in record time at the Royal Free London (RFL) this week – with the first 200 bottles ready for use on the wards.
The trust’s pharmacy team took just four days to begin manufacturing the new product – setting up a new process would normally take up to six months.
Jasdeep Singh, RFL principal pharmacist, said: “We saw there was a shortage and that it might not be sorted quickly so we had to do something to help try to stop the spread of the virus and protect people.
“There’s a lot about this crisis which is about innovation and being nimble. We were glad to be able to respond quickly to the issue.”
The hand sanitiser formula was supplied by the World Health Organization and the 500ml bottles are being produced by the trust’s manufacturing pharmacy - the previous week it had produced 20ml packs for individual members of staff.
Both external agencies and internal departments that needed to approve the product were able to give a speedy green light to the new sanitiser so that production could get going promptly.
Jasdeep added: “It was good to see that people understood the problem and how we could help to fix it. They worked as quickly as they could, being as pragmatic as they could without compromising on safety, effectiveness or quality.”
In total 13 pharmacy staff were involved in the process, as well as colleagues in other departments including quality assurance and infection control, who ensured the solution worked and was safe. Clarissa Coker, the quality assurance lead, and Alan Sebti, the manufacturing and procurement lead, together with support from Vicky Pang, the infection control lead, ensured a speedy process.
Image: Pharmacy team member Dr Blanka Gonczy